Wouldn't that be cool?! Part 1
- Daughter Mfg
- Oct 3, 2023
- 3 min read
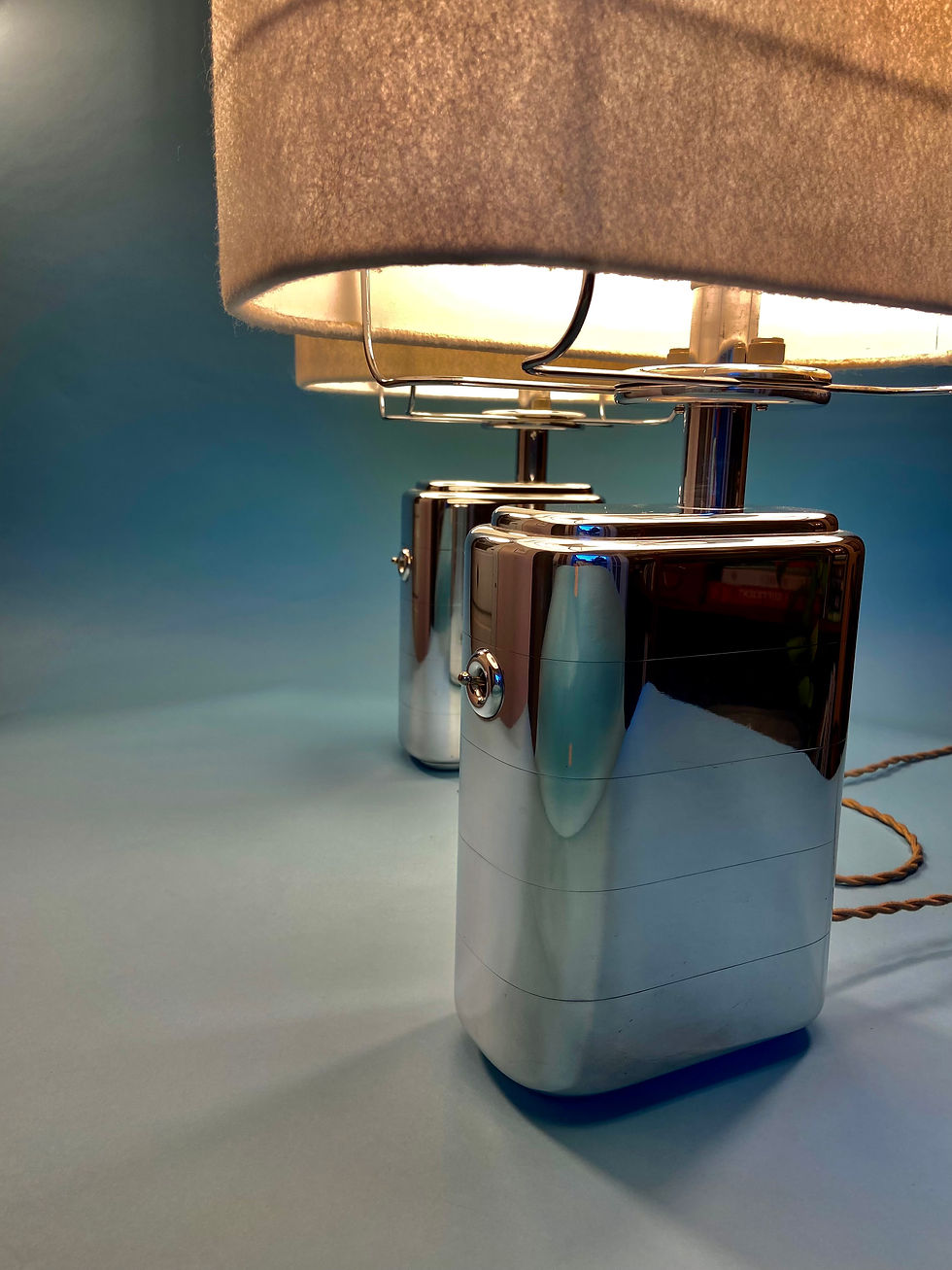
Our Empire Lamp project originated back in 2015 out of a desire to do something in line with an era we dearly love that’s often referred to as Art Deco, Moderne or Streamline.
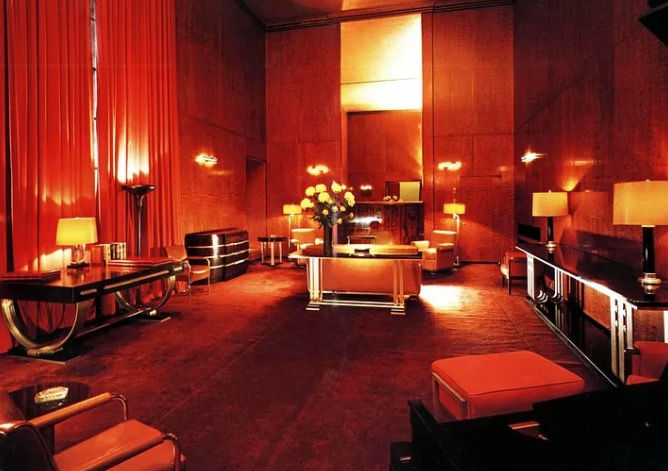
We’ve often thought of the office that Donald Deskey designed for Radio City Music Hall as one of our favorite interiors and, after visiting the Empire State Building on a family trip, we started talking about what a lamp for one of these interiors could look like, something that was sleek and refined and looked at home sitting on a polished walnut desk in an executive’s office in the 1930’s, but that could still work in a present day home that was not ultra-modern.
We tossed around many ideas and concepts over a period of time. We agreed that there’s really nothing quite like the look of silvery polished metal. Mario being a machinist, he's always felt a real kinship with aluminum. Oh, and rounded corners! And so that’s where we started, with just those rough ideas. After a lot of sketching and looking through scores of books and magazines for inspiration, Mario roughed out a profile/concept late one night that seemed like it could have possibilities. Mainly, it was just the oblong body shape and the offset stem leading into a boxy shade.
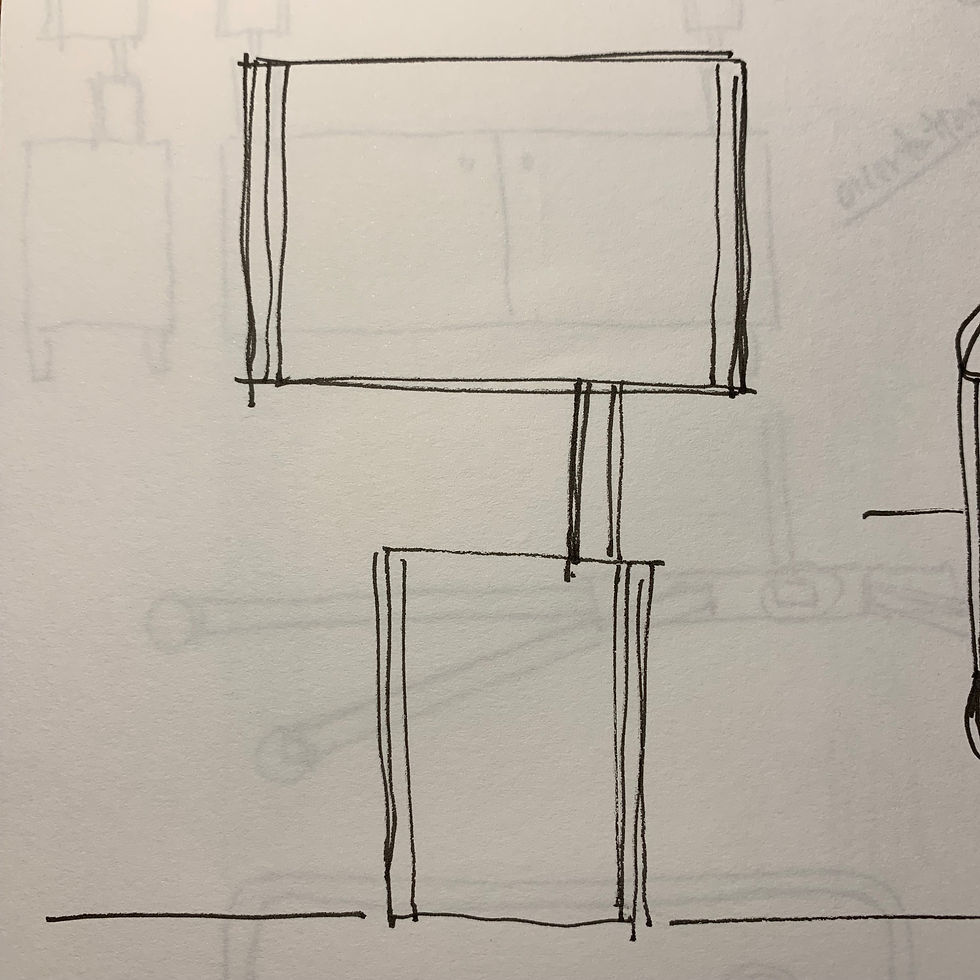
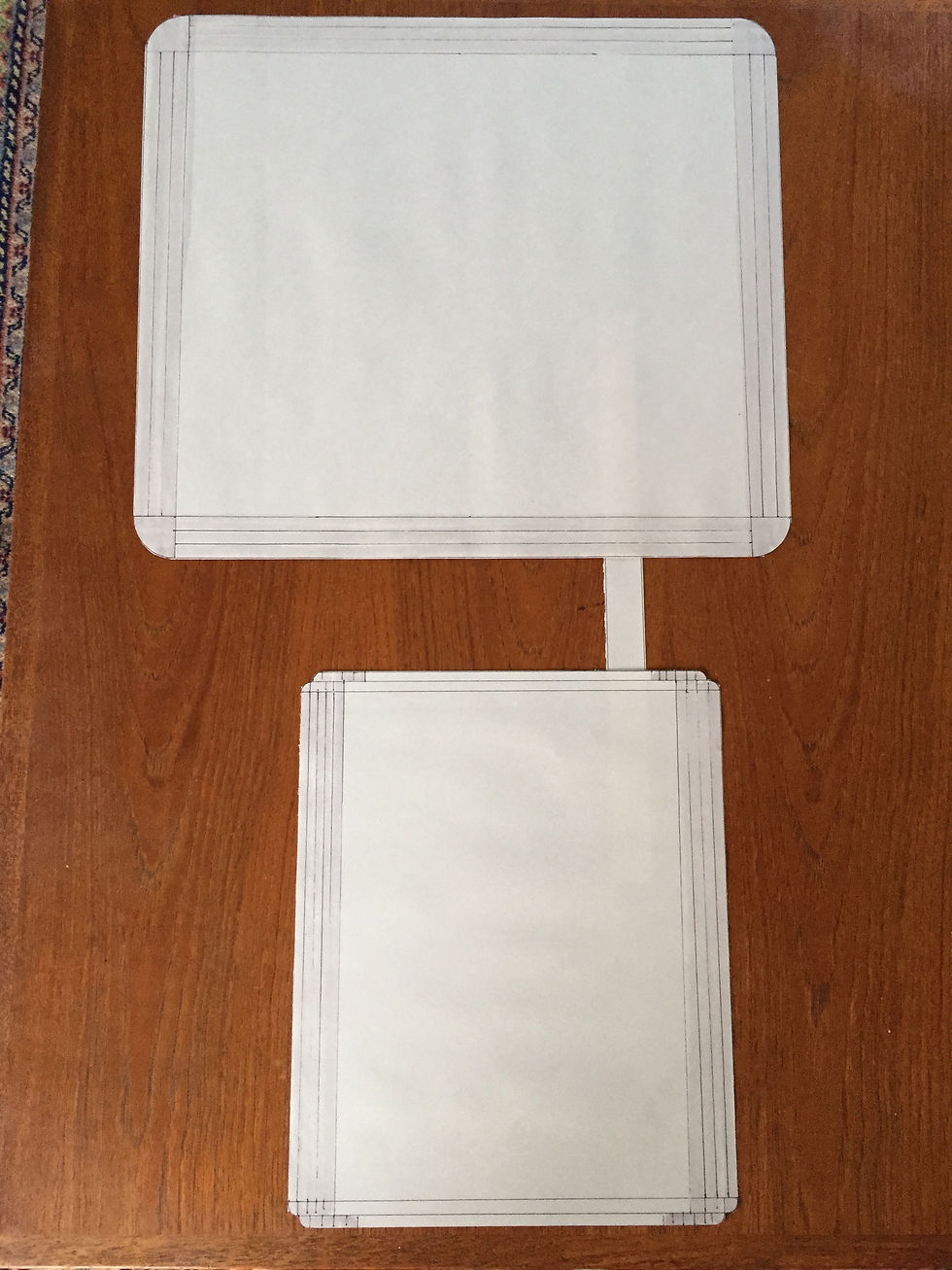
There was one not so small issue, though - we had just moved into a very small house in Silicon Valley and had no equipment, no place to work, just a dining room table under a carport to lay things out. It felt like playing pretend, but we just started. We started by making computer renderings and awkward foam and birch prototypes.

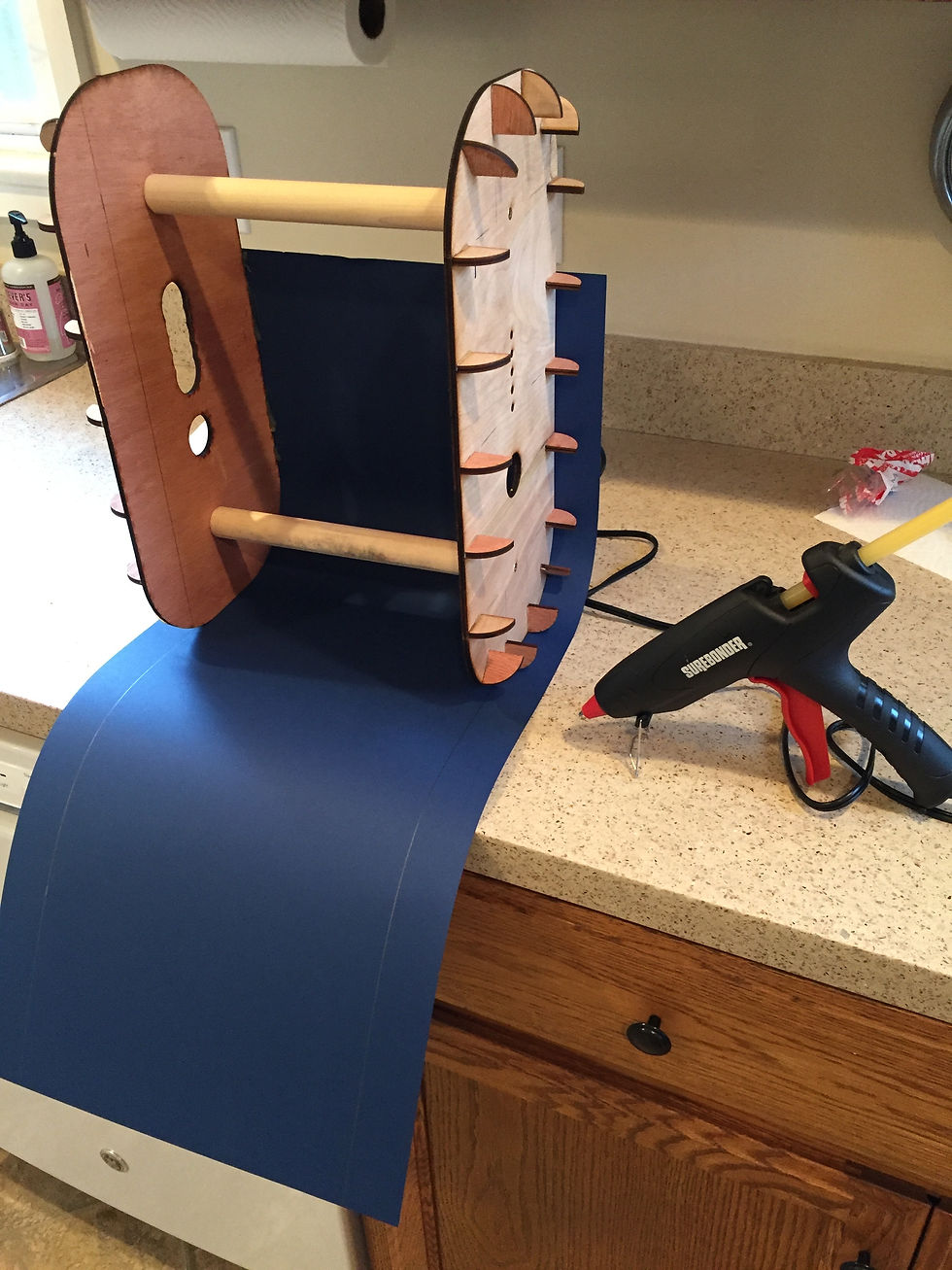
What was most frustrating for us was that the manufacture of the lamp was front-and-center in our minds during the design process and greatly influenced how it presented aesthetically, but that we couldn’t actually make it ourselves owing only to a lack of equipment and space, certainly not the know-how.
So we had to turn to some local vendors to help us realize the project, providing them with CAD models, working drawings and some notes about what we wanted. A local machine shop Mario had worked with before made several of the parts for us, including "slices" of the extrusion body that were press-fit together using dowel pins (more on that later). We worked with a company in Los Angeles that specialized in wire fabrication to make four different shade prototypes for us, which we then had covered by a retired couple who worked out of their home in Monterey.
After a few months of coordination, we finished two of the prototypes and that we have now lived with for 8 years.
That’s a long time to live with and interact with a prototype and we’ve only grown more fond of them over time. But it’s exactly what helped us decide to make this our first project;
a design that stood the test of time for us and a design unique to us that would be an honest way to introduce ourselves to the world.
When we say that if only we had had the necessary tools and space to make the design, we would have done it ourselves, that is not entirely true. There is only one efficient way to make the body of the lamp and it is through a process called extrusion. Only vendors with very large industrial facilities and equipment and specialized knowledge of the process involved could do this for us. And it would be hilariously expensive.
More on that in "Oh, we can do this! Part 2" coming at the end of the month.
Comments